QUALITY


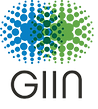

The Quality approach that we put in place implies a constant motivation of all the staff.
It's a real way of life.
In addition to our qualifications / accreditations, SMEPI is a member of the various nuclear associations:

Documentation
SMEPI has positioned itself as one of the major players in the energy sector in France and particularly in the nuclear sector by mastering the RCC-M code, its document management and its quality processes.
We are able to provide you with prior written request, the traceability of your parts, according to your requirements:
​
-
CCPU3.1
-
Quality plan
-
End of production report (RFF).
​
The traceability documents are archived according to the conditions of our procedure 1.2.6 and are available on our premises upon written request.

Tracability
Certified ISO 9001 V2015, SMEPI undertakes according to the contractual requirements, to ensure a perfect traceability of its files of manufacture: from the origin of the raw material, until the declaration of conformity of the part, while passing by the calibration's certificate of the measuring means.
Each customer benefits from a single point of contact, who takes care of the follow-up of his orders from the launch in manufacturing until the delivery of the parts on site.
To do this, management is carried out through Clipper, our CAFM system .

Quality control of safety and security
Aware of the security issues related to the areas of application of its customers' rooms (nuclear power plant, thermal, amusement park ...), SMEPI is committed to providing services that meet the requirements of its customers and meet security requirements and reliability.
Its staff therefore regularly participate in training sessions on safety and security.
Our company has a control room under controlled atmosphere at a temperature of 20 ° C, equipped with multiple measuring devices (ROMER Arm, Contourograph, Magnetic Bench, Mass Spectrometer ...).
This room allows the realization of inspection / recipe, in the presence of our customers, to validate a manufacturing stage, as required by the reference of certain parts (RCC-M).
In accordance with customer specifications, many controls are carried out internally. Non-destructive tests are carried out by COFREND I and II certified personnel.
-
Dimensional and Visulal Control
-
Chemcal analysis
-
Hardness Test
-
Resilience Test
-
Trial Load Test
-
Review by Ultra-Sounds
-
Review by Ressuage
-
Review by Magnetic particle
Our machined parts are systematically checked (1st part control + control during production) by our quality department. The metrology of our measuring instruments is monitored via dedicated Gessica software.
Calibration campaigns are carried out regularly via the skills and experience of accredited COFRAC laboratories.